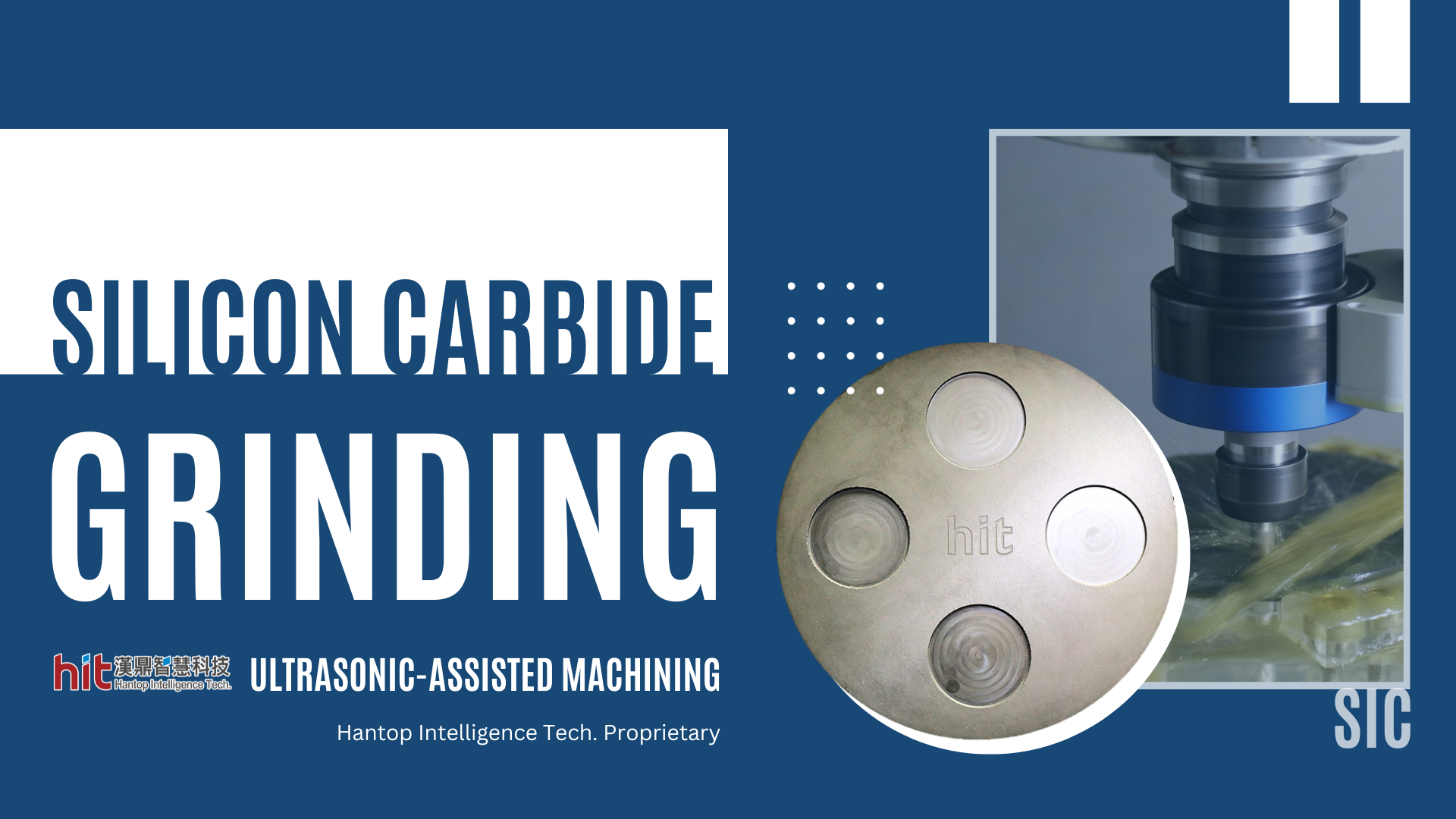
What Does HIT Ultrasonic Machining Bring to Silicon Carbide (SiC) Grinding?
[Ultrasonic High Frequency Oscillation]
HIT's ultrasonic-assisted machining technology provides the superimposition of the tool rotation with a high-frequency oscillation in longitudinal direction, generating over 20,000 times of micro-vibration per second. The mechanism helps reduce grinding forces and facilitates ceramic particle flushing. The high-frequency oscillation in longitudinal direction allows for an intermittent contact between the tool and workpiece. This helps eliminate accumulative heat around the grinding tool, which results in great reduction in tool wear.
[Reduction in Grinding Forces]
The reduction in grinding forces not only decreases frictions between the tool and workpiece, but also allows cutting speed and feed rate to be increased. This mechanism also helps lower the heat generated during the machining process. It greatly improves the workpiece quality and stability in tool life and saves a huge amount of energy and total process time.
[Better Particle Flushing]
Facilitating ceramic particle flushing also reduces frictions on both tool and workpiece caused by excessive particles stuck on the grinding tool/wheel. If the pores (between abrasives) of the grinding tool were filled with accumulative ceramic particles, the tool would quickly lose its grinding ability.
The high frequency micro-vibration of ultrasonic brings better particle flushing, which helps generate the self-sharpening mechanism (worn-out abrasive grits fall off, and new diamond grits come out to continue grinding) of grinding tool/wheel. This can greatly reduce the time and tool wear from tool dressing process.
[Ultrasonic High Frequency Oscillation]
HIT's ultrasonic-assisted machining technology provides the superimposition of the tool rotation with a high-frequency oscillation in longitudinal direction, generating over 20,000 times of micro-vibration per second. The mechanism helps reduce grinding forces and facilitates ceramic particle flushing. The high-frequency oscillation in longitudinal direction allows for an intermittent contact between the tool and workpiece. This helps eliminate accumulative heat around the grinding tool, which results in great reduction in tool wear.
[Reduction in Grinding Forces]
The reduction in grinding forces not only decreases frictions between the tool and workpiece, but also allows cutting speed and feed rate to be increased. This mechanism also helps lower the heat generated during the machining process. It greatly improves the workpiece quality and stability in tool life and saves a huge amount of energy and total process time.
[Better Particle Flushing]
Facilitating ceramic particle flushing also reduces frictions on both tool and workpiece caused by excessive particles stuck on the grinding tool/wheel. If the pores (between abrasives) of the grinding tool were filled with accumulative ceramic particles, the tool would quickly lose its grinding ability.
The high frequency micro-vibration of ultrasonic brings better particle flushing, which helps generate the self-sharpening mechanism (worn-out abrasive grits fall off, and new diamond grits come out to continue grinding) of grinding tool/wheel. This can greatly reduce the time and tool wear from tool dressing process.
Hantop Intelligence Technology
Brand Name:
Hantop Intelligence Technology
Booth Number :
P1232
Contact Information :
- www.hit-tw.com
- +886-4-22850838
- +886-4-22850836
- Room 921, Applied Science & Tech. Building, No. 145 Xingda Road, South District, Taichung City 402, Taiwan